What’s New in Anti-Corrosion Technologies for Pressure Vessels in Ocala, Florida?
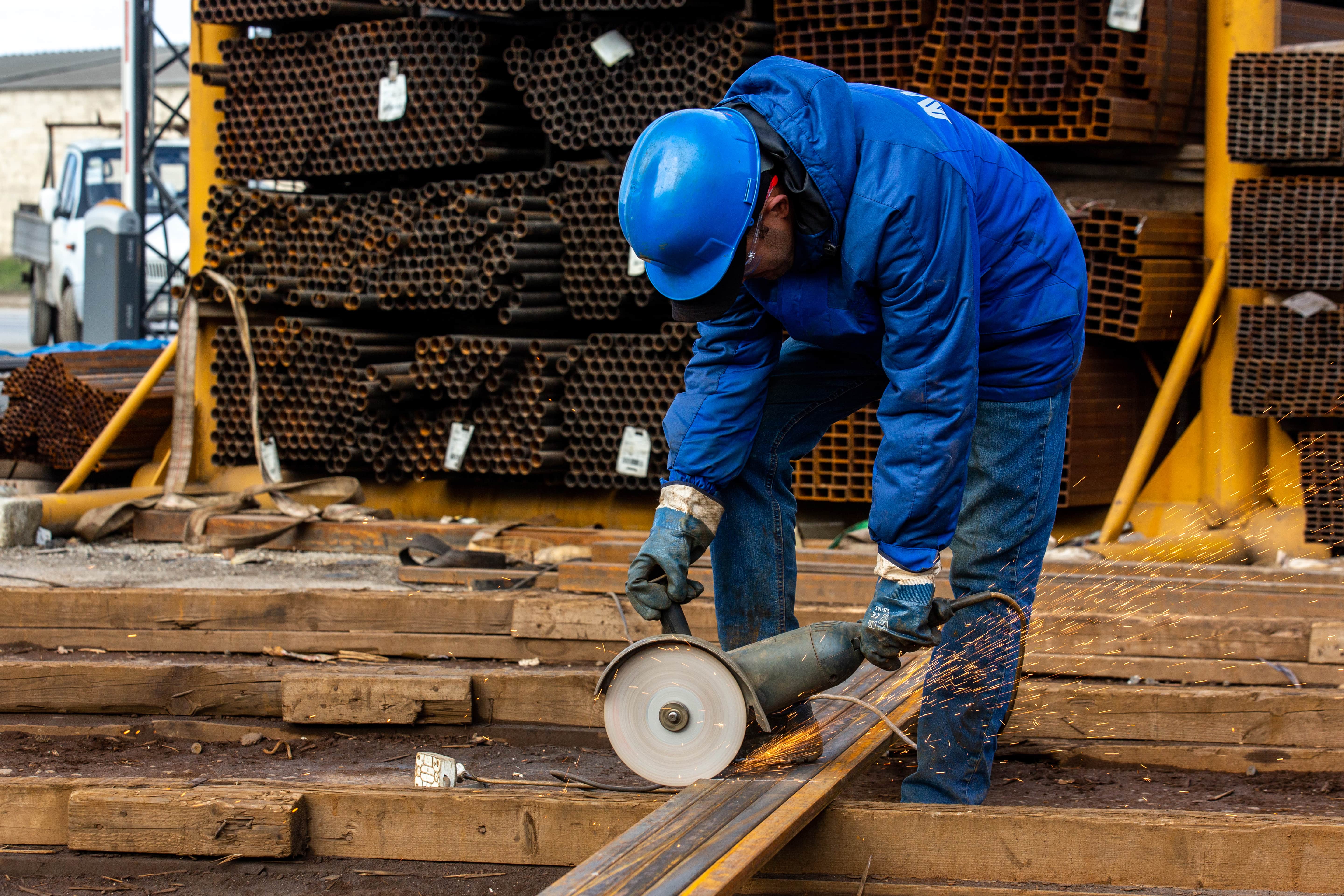

What’s New in Anti-Corrosion Technologies for Pressure Vessels in Ocala, Florida?
1. High-Performance Coatings with Self-Healing Capabilities
Protective coatings have long been a go-to solution for corrosion prevention. However, self-healing coatings are setting new industry standards by offering an automatic repair mechanism when damage occurs. These coatings contain microcapsules filled with corrosion inhibitors or polymeric healing agents, which release upon impact or scratches, sealing exposed areas and preventing further oxidation.
Types of Self-Healing Coatings:
- Polymer-Based Coatings: Use epoxy or polyurethane microcapsules to self-repair surface cracks.
- Graphene-Infused Coatings: Provide enhanced durability and electrical conductivity to prevent oxidation.
- Ceramic-Based Coatings: Offer excellent heat and chemical resistance, ideal for high-temperature applications.
These coatings significantly reduce maintenance costs and increase service life, making them a preferred choice for harsh industrial environments.
2. Advanced Surface Treatments: Plasma Electrolytic Oxidation (PEO)
Traditional surface treatments like galvanization and anodization have their limitations. Plasma Electrolytic Oxidation (PEO) is an emerging technique that creates a ceramic-like oxide layer on metal surfaces, offering superior corrosion resistance.
Key Benefits of PEO:
- Forms a hard, durable surface layer that withstands extreme conditions.
- Stronger adhesion properties, ensuring longer-lasting protection.
- Excellent resistance to high temperatures and chemical exposure.
PEO is particularly effective for aluminum and titanium pressure vessels, commonly used in aerospace, medical, and marine applications.
3. Nanotechnology-Based Corrosion Inhibitors
Nanotechnology is making corrosion prevention more precise and efficient. Nano-coatings and nano-additives are engineered at the molecular level to enhance surface protection by blocking moisture, oxygen, and corrosive chemicals.
How Nano-Coatings Work:
- Silica and titanium dioxide nanoparticles reinforce coatings to improve strength and flexibility.
- Carbon nanotube-infused coatings prevent oxidation and enhance thermal stability.
- Superhydrophobic (water-repelling) nanocoatings reduce moisture-related corrosion.
These coatings are particularly useful in industries that deal with chemicals, saltwater, or extreme environmental conditions, such as pharmaceutical manufacturing, petrochemicals, and marine engineering.
4. Corrosion-Resistant Alloy Development
While coatings provide an external barrier, using corrosion-resistant alloys (CRAs) ensures long-term protection at the material level. Newer alloy compositions are being developed to withstand highly corrosive environments without requiring extensive maintenance.
High-Performance Alloy Options:
- Super Duplex Stainless Steel (SDSS): Superior resistance to chloride-induced corrosion.
- Nickel-Aluminum Bronze: Exceptional durability in seawater and acidic environments.
- Titanium Alloys: Highly resistant to oxidation, used in power plants and desalination units.
CRAs help reduce dependence on coatings, making them a cost-effective solution for pressure vessels in highly aggressive industrial conditions.
5. Smart Corrosion Monitoring Systems
Advancements in IoT-based monitoring are transforming corrosion management. Traditional inspections rely on manual checks, but real-time smart monitoring systems now allow for continuous assessment of metal degradation.
New Monitoring Technologies:
- Electrochemical Impedance Spectroscopy (EIS): Measures the electrical resistance of coatings to detect early signs of corrosion.
- Fiber Optic Sensors: Monitor moisture levels, temperature, and pH changes inside pressure vessels.
- AI-Powered Predictive Maintenance: Uses machine learning to analyze corrosion trends and predict failures before they occur.
By integrating smart corrosion detection, industries can optimize maintenance schedules, reduce downtime, and prevent catastrophic failures.
6. Hybrid Coating Systems for Extreme Environments
To withstand high-pressure, high-temperature, and chemically aggressive conditions, hybrid coatings are gaining traction. These coatings combine multiple protective technologies to create multi-layered protection.
Examples of Hybrid Coatings:
- Ceramic-Polymer Coatings: Merge ceramic durability with polymer flexibility to resist cracking.
- Multi-Layer Epoxy-Zinc Coatings: Combine zinc’s sacrificial properties with epoxy’s strong adhesion.
- Thermal Spray Coatings: Provide a heat-resistant, corrosion-inhibiting barrier.
Hybrid coatings are ideal for offshore drilling, energy plants, and heavy chemical industries.
7. Electrochemical Protection with Next-Gen Cathodic Protection Systems
Cathodic protection (CP) is a widely used electrochemical technique to prevent metal corrosion. Recent innovations have made CP more efficient, cost-effective, and long-lasting.
Latest Innovations in CP Systems:
- Self-Powered CP Systems: Utilize solar panels or energy-harvesting technologies to operate in remote locations.
- Advanced Anode Materials: Mixed-metal oxides and conductive polymers provide longer-lasting corrosion protection.
- AI-Optimized CP Adjustments: Smart systems adjust voltage and current dynamically based on environmental conditions.
These advancements are particularly beneficial for underground storage tanks, marine vessels, and pipelines, where coatings alone are not enough for long-term corrosion prevention.
Why These Innovations Matter for Ocala, Florida
Industries in Ocala, Florida, especially those involved in manufacturing, aerospace, agriculture, and water treatment, rely on pressure vessels for critical operations. Given the region's high humidity and industrial exposure, investing in advanced corrosion prevention strategies ensures long-term performance, compliance with safety regulations, and cost savings.
Key Takeaways for Businesses in Ocala:
Reduce Maintenance Costs – New self-healing and nano-coatings minimize frequent inspections and repairs.
Extend Service Life – Corrosion-resistant alloys and hybrid coatings enhance durability.
Improve Safety & Compliance – Smart monitoring systems help industries comply with ASME and NACE standards.
Prevent Unexpected Failures – Predictive maintenance and cathodic protection systems eliminate downtime risks.
Conclusion
Advancements in anti-corrosion technologies are revolutionizing pressure vessel durability, offering stronger coatings, smarter monitoring, and better material choices. Industries in Ocala, Florida, can benefit from adopting these innovations to prevent costly corrosion damage, maintain operational efficiency, and meet compliance standards.
As technology evolves, more sophisticated anti-corrosion solutions will continue to emerge, providing safer and more reliable pressure vessel systems for industrial applications.
For businesses in Ocala, Florida, looking to enhance the corrosion resistance of their pressure vessels, consulting with industry experts can make all the difference. The specialists at Alien Engineered Products (AEP) offer tailored corrosion prevention strategies, custom fabrication, surface treatment, and advanced monitoring solutions to help industries optimize the lifespan and performance of their equipment.
Get in Touch with the Experts at AEP
To learn more about custom anti-corrosion solutions, pressure vessel fabrication, or consultation services, reach out to Alien Engineered Products (AEP) in Ocala, Florida today.