How Custom Pressure Vessel Fabrication Enhances Industrial Efficiency
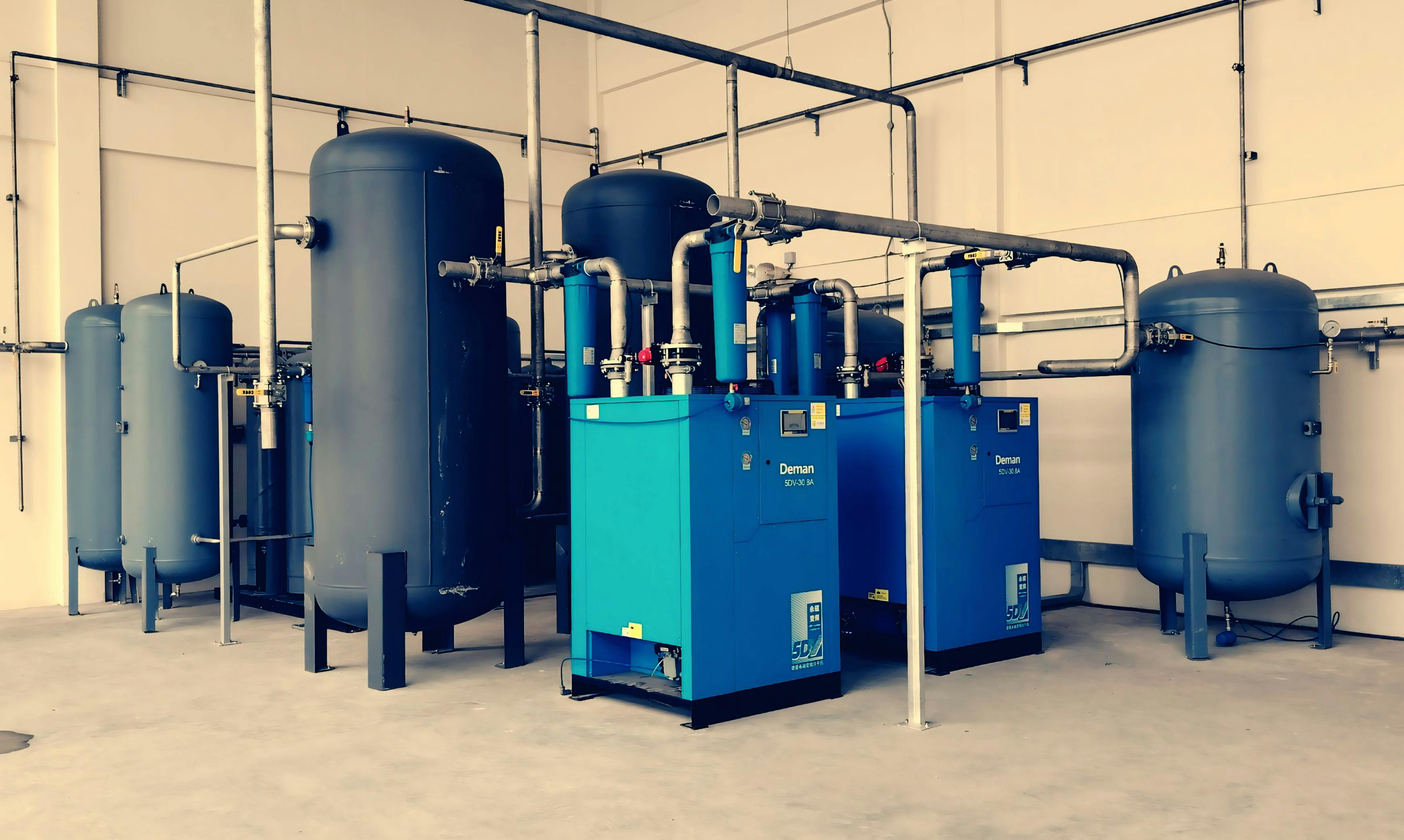

How Custom Pressure Vessel Fabrication Enhances Industrial Efficiency
1. Tailored Pressure Vessel Design for Process Optimization
Off-the-shelf pressure vessels are made to accommodate general needs. However, industrial operations often have unique variables: specific temperature ranges, pressure levels, flow rates, and chemical compositions. Custom-fabricated pressure vessels allow engineers to tailor design parameters precisely to match operational goals.
Key benefits include:
- Optimized geometry for improved fluid dynamics
- Exact placement of nozzles, baffles, and manways
- Seamless integration with existing plant infrastructure
This level of customization ensures smoother operations, faster throughput, and minimal energy loss—directly impacting overall plant performance and efficiency.
2. Material Selection Based on Application-Specific Requirements
Every industrial process has different corrosion, temperature, and pressure demands. Custom pressure vessel manufacturers offer flexibility to choose materials that align perfectly with these variables.
Common material options include:
- Stainless steel for sanitary processing and hygienic design
- Carbon steel for high-pressure gas storage
- Inconel and Hastelloy for high-temperature and corrosive environments
By selecting the right material for the job, industries reduce equipment failure rates and minimize unplanned downtime.
3. Improved Heat Transfer and Energy Efficiency
Heat exchange is central to many industrial manufacturing processes. Custom vessels can be engineered with thermal jackets, internal coils, or insulation layers that promote efficient heat transfer.
Advantages:
- Quicker heating and cooling cycles
- Reduced overall energy consumption
- Better control over process temperatures
These enhancements lower operating costs and support sustainability initiatives through energy conservation.
4. Pressure Vessel Fabrication for Space Optimization
Space constraints are common in industrial facilities. Standard vessels often don’t fit efficiently within floor plans, creating inefficiencies in piping layouts and access.
Custom-fabricated vessels can be:
- Configured vertically or horizontally
- Scaled to match exact volume and space requirements
- Mounted on modular skids for ease of relocation
This results in reduced installation time, easier maintenance access, and better use of available workspace.
5. Smart Integration with Industrial Automation Systems
Modern facilities rely on automation and control systems to drive efficiency. Custom fabrication ensures that pressure vessels come ready for integration with:
- IoT-enabled sensors for temperature and pressure
- SCADA and PLC systems for real-time monitoring
- Smart valves and flow control units
This connectivity allows for predictive maintenance, operational analytics, and improved safety monitoring.
6. Downtime Reduction with Service-Friendly Features
Unplanned downtime is one of the most costly challenges for industrial operations. Custom fabrication enables design enhancements such as:
- Removable heads and manways for quick internal access
- Bolt-on thermal jackets for easy maintenance
- Modular construction for rapid disassembly and repair
By reducing service time and streamlining maintenance, these features directly improve equipment availability and reduce overall lifecycle costs.
7. Compliance with ASME, PED, and Industry Standards
Compliance is critical for avoiding penalties and ensuring operational safety. Reputable pressure vessel fabricators build custom units in line with global standards:
- ASME Section VIII for North America
- PED 2014/68/EU for the European market
- cGMP compliance for pharmaceutical-grade equipment
Custom fabrication allows for pre-built documentation, validation, and quality assurance that simplify regulatory inspections and audits.
8. Reducing Long-Term Costs Through Durability and Custom Fit
While custom-built vessels may have a higher upfront cost, they yield better return on investment (ROI) by:
- Lasting longer due to material and process compatibility
- Lowering maintenance costs
- Reducing energy waste from heat loss or frictional inefficiencies
Industries benefit from higher productivity, fewer breakdowns, and better cost control over time.
9. High-Performance Vessels for Hazardous Environments
In sectors like oil & gas, chemical processing, and nuclear energy, safety and durability are non-negotiable. Custom-fabricated pressure vessels can be tailored with:
- Dual-containment walls
- Explosion-proof linings
- Purging systems and fail-safe venting
These features protect workers and infrastructure, while ensuring operations continue smoothly under demanding conditions.
10. Enabling Lean Manufacturing with Custom Pressure Vessels
Lean manufacturing emphasizes reducing waste and increasing value. Custom pressure vessels contribute to lean operations by:
- Eliminating oversized or underutilized components
- Reducing material and energy waste
- Improving overall equipment effectiveness (OEE)
This leads to streamlined production lines, improved cycle times, and optimized throughput.
Conclusion
Custom pressure vessel fabrication services are more than a design preference—they're a performance upgrade. By aligning vessel design, materials, and functionality with the specific requirements of each operation, industries gain better control, reduced downtime, and improved operational efficiency.
From energy savings and regulatory compliance to smarter automation and leaner processes, custom vessels provide measurable advantages. When engineered to spec, pressure vessels become integral components of a high-efficiency plant.
Interested in boosting your plant’s efficiency with precision-engineered pressure vessels?
Reach out to the experts at Alien Engineered Products, a trusted name in custom metal fabrication for pressure vessels. Our engineers will work with you to create tailor-made solutions that deliver results. Contact us today to learn more.