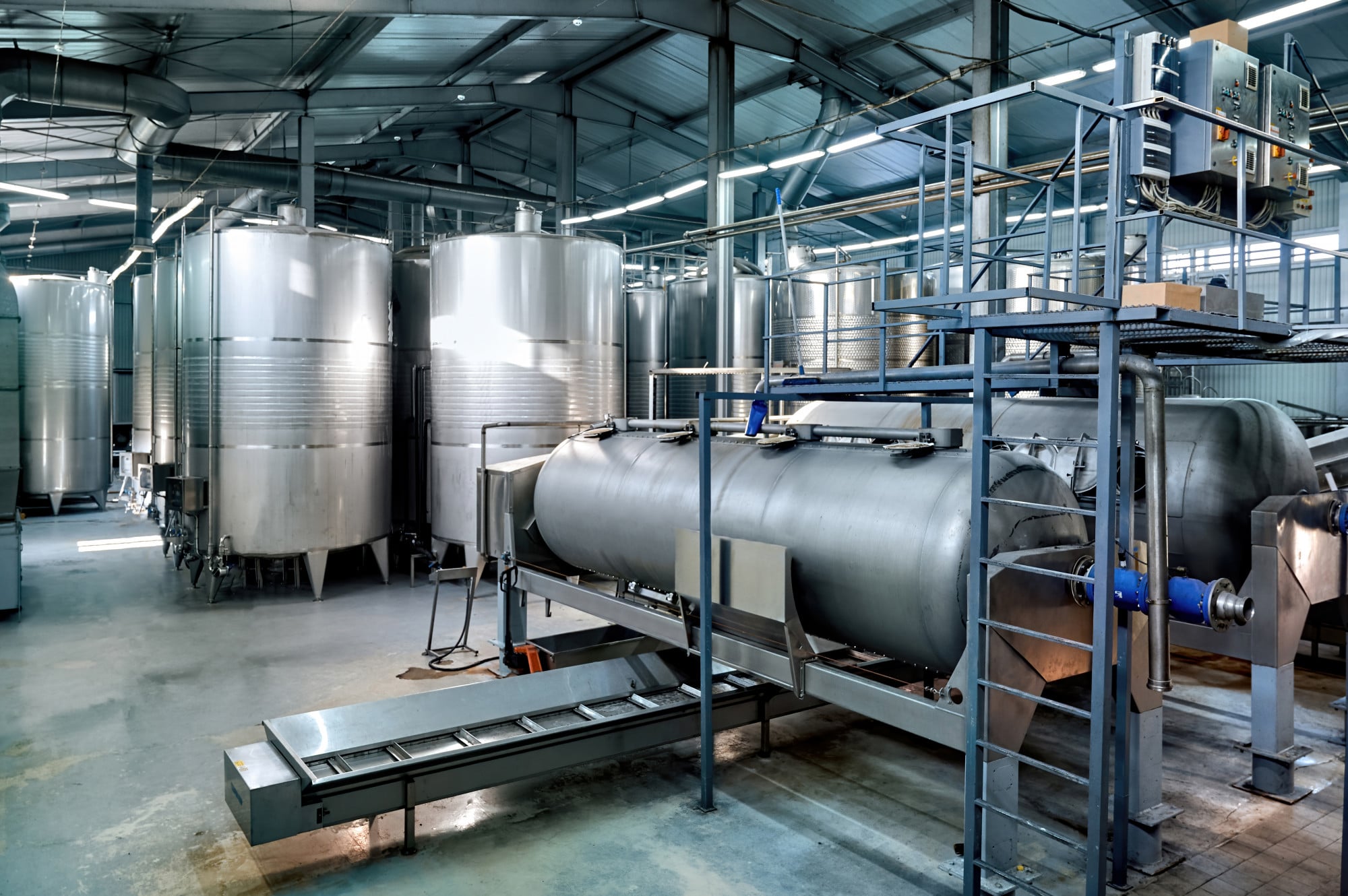

How to Maintain and Inspect Your Pressure Vessel for Longevity
1. Align Maintenance Schedules with Design Conditions
Begin by reviewing the vessel’s design specifications:
- Operating pressure and temperature
- Corrosion allowance and material type (e.g., stainless steel, carbon steel)
- Frequency of cycles (thermal, pressure)
- Service media (gas, liquids, corrosive substances)
Matching your pressure vessel maintenance schedule to these conditions is vital to avoid premature wear and support long-term reliability.
2. Apply Risk-Based Inspection (RBI) Strategies
Risk-based inspection (RBI) allows you to prioritize inspection efforts based on:
- Probability of failure (based on environment, history, material)
- Consequence of failure (safety, environmental, production loss)
This method ensures high-risk vessels receive more frequent and thorough inspections, helping with pressure vessel failure prevention.
3. Conduct Regular External Pressure Vessel Inspections
Monthly or quarterly external pressure vessel inspections can identify early signs of deterioration. Focus on:
- Paint/coating condition (especially for carbon steel vessels)
- Visible corrosion or rust
- Weld seam integrity
- Leaks around nozzles and joints
- Base and support structure condition
These inspections are essential for early pressure vessel repair planning.
4. Perform Scheduled Internal Pressure Vessel Inspections
Every 3 to 5 years, conduct an internal pressure vessel inspection to examine:
- Pitting or scaling on internal surfaces
- Signs of fatigue or stress cracking in welds
- Coating or liner degradation
- Deposit accumulation or erosion in high-flow areas
Ensure adherence to confined space entry procedures, including proper ventilation, gas detection, and supervision.
5. Use Non-Destructive Testing (NDT) Techniques
To go beyond visual inspections, apply non-destructive testing (NDT) for a deeper analysis:
- Ultrasonic Testing (UT): Measures wall thickness and detects internal thinning
- Radiographic Testing (RT): Identifies internal weld defects
- Magnetic Particle Inspection (MPI): Detects surface and near-surface cracks in ferromagnetic materials
- Dye Penetrant Testing (DPT): Highlights surface cracks in non-ferrous materials
These NDT methods are critical for identifying hidden risks and planning timely interventions.
6. Monitor Corrosion and Track Wall Thickness
Corrosion monitoring involves tracking material loss using UT over time. Create a corrosion log that includes:
- Baseline and current thickness readings
- Annual corrosion rate
- Minimum allowable wall thickness
Use this data to plan maintenance and prevent exceeding code-defined limits. Understanding how to calculate pressure vessel corrosion rate is key for predicting remaining life.
7. Service and Inspect Pressure Relief Valves (PRVs)
Pressure relief valve (PRV) maintenance is a critical component of vessel safety. PRVs must be:
- Calibrated and tested annually (or per OEM guidelines)
- Checked for blockages or corrosion
- Inspected for leaks and reseating issues
Understanding how often pressure relief valves should be inspected is vital for maintaining safety and compliance.
8. Maintain Detailed Maintenance Records
Document all inspections and repairs in a digital log or CMMS system. Include:
- NDT reports and wall thickness testing data
- Inspection frequencies and RBI classifications
- PRV certification and calibration logs
- Notes from internal and external inspections
Knowing how to document pressure vessel maintenance supports audits and operational planning.
9. Plan for Re-Rating When Conditions Change
A change in service conditions (e.g., pressure, temperature, medium) may require a pressure vessel re-rating. This involves:
- Updated calculations under ASME Section VIII or PED 2014/68/EU
- Re-inspection and documentation
- Potential re-certification through third-party agencies
Unplanned operation beyond design conditions can lead to compliance violations and reduced safety.
10. Train Maintenance Personnel on Pressure Vessel Safety
Technicians should be trained on:
- Basic vessel design and specifications
- Inspection techniques and warning signs
- Safe operation and entry procedures
- NDT basics and recordkeeping
This supports a culture of pressure vessel safety and reduces risk.
1. How to perform pressure vessel inspection?
A complete pressure vessel inspection involves visual checks, NDT (UT, RT, MPI, DPT), and internal examination under confined space protocols. Frequencies depend on service conditions and RBI classification.
2. What are the signs of pressure vessel failure?
Common indicators include corrosion, wall thinning, leakage at nozzles, bulging or deformation, and pressure relief valve malfunction.
3. How often should pressure relief valves be inspected?
Most standards recommend annual testing and calibration, but inspection frequency should be based on system criticality and service environment.
4. What are the ASME standards for pressure vessel inspection?
ASME Section VIII outlines requirements for design, testing, and inspection. Inspections should align with code-defined intervals, thickness tolerances, and safety margins.
5. What are best practices for pressure vessel corrosion monitoring?
Use UT to measure wall thickness regularly, track corrosion rate, and compare against minimum design thickness. Clean vessels periodically to remove buildup that accelerates corrosion.
6. What are the steps for internal pressure vessel inspection?
Drain and depressurize the vessel, follow confined space entry protocols, visually inspect internal surfaces, test for pitting and cracking, and document findings with photographs and measurement data.
Certified ASME and PED Pressure Vessel Manufacturing
Alien Engineered Products (AEP) specializes in the manufacture of custom pressure vessels that meet rigorous international standards, including ASME Section VIII and PED 2014/68/EU. If you're looking for a trusted partner to fabricate pressure vessels tailored to your specifications, AEP delivers certified, high-quality solutions built for long-term performance and code compliance.
Ready to start your next pressure vessel project?
Get in touch with our team to request a quote or discuss your requirements for ASME-certified and PED-compliant pressure vessels. Let’s build something that lasts.