Preventing Pressure Vessel Failure Through Reliable Maintenance Practices for International Markets
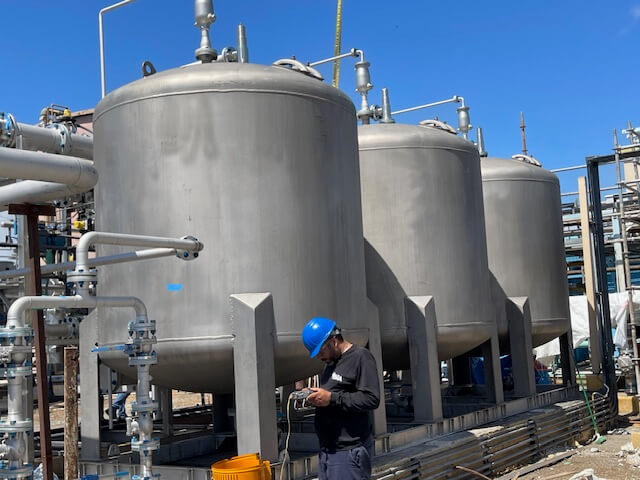

Preventing Pressure Vessel Failure Through Reliable Maintenance Practices for International Markets
The Grave Consequences of Pressure Vessel Failure
Pressure vessel failures are more than operational setbacks—they can be life-threatening events with dire financial and reputational repercussions. From damaged infrastructure and prolonged plant shutdowns to severe injuries or even fatalities, the stakes are undeniably high. Furthermore, incidents involving pressure vessel explosions can disrupt supply chains, lead to costly litigation, and damage a company's reputation irreparably.
Establishing a preventive maintenance strategy aligned with stringent European standards like the PED is essential for mitigating these risks. Proactive maintenance not only ensures vessel safety but also optimizes operational efficiency over the long term.
European Standards and Regulations for Pressure Vessel Maintenance
To uphold the highest levels of safety and reliability, pressure vessels must adhere to a robust framework of international and European regulations. These standards ensure vessels are manufactured, maintained, and inspected with unparalleled precision.
Pressure Equipment Directive (PED) – EU Compliance
In Europe, the PED sets the gold standard for pressure equipment operating above 0.5 bar. Compliance with the PED is a legal necessity, aimed at harmonizing safety practices across all EU member states. AEP’s pressure vessels are rigorously engineered and tested to meet or exceed PED requirements, guaranteeing safety and performance.
ASME Standards
Although more prevalent in North America, many global operations in Europe still follow ASME codes. These standards complement the PED and cover detailed design, material selection, and testing protocols.
At AEP, we commit to these standards, particularly the PED, integrating them into every aspect of our pressure vessel design, engineering, and maintenance processes.
The Core of PED Compliance
Understanding PED compliance is crucial for companies operating within the EU. Here’s what it entails:
Design and Analysis
Under the PED, pressure vessels must undergo rigorous design verifications, such as stress analysis and fatigue testing. These processes ensure vessels can endure expected operational conditions. At AEP, we use advanced simulation tools to validate designs, prioritizing structural integrity and reliability.
Material Specifications
The PED mandates stringent quality checks on all materials, requiring them to withstand extreme pressures and harsh environmental factors. AEP selects premium, corrosion-resistant materials and subjects them to thorough testing to ensure durability and PED compliance.
Documentation and Inspections
The PED emphasizes exhaustive documentation of maintenance activities and routine inspections throughout a pressure vessel's life cycle. Each maintenance operation, whether scheduled or emergency, must be meticulously recorded for future audits. AEP’s comprehensive maintenance protocols keep clients compliant and prepared for regulatory checks.
Our commitment to PED compliance extends beyond manufacturing, encompassing quality assurance, documentation, and dedicated customer support.
Best Practices for Pressure Vessel Maintenance in Europe
Preventive maintenance is the key to ensuring safety and prolonging the lifespan of pressure vessels. AEP follows best practices rooted in PED guidelines to keep vessels operational and compliant:
Regular Inspections
Routine inspections detect early signs of corrosion, material fatigue, or structural anomalies. Techniques like visual checks and ultrasonic testing assess the vessel's condition comprehensively. AEP conducts these inspections systematically, helping clients preempt costly failures.
Non-Destructive Testing (NDT)
Methods like radiographic testing, ultrasonic flaw detection, and magnetic particle inspection are essential for identifying hidden defects without compromising the vessel’s structure. AEP leverages the latest NDT technology to ensure structural integrity and compliance.
Pressure and Temperature Monitoring
Consistent monitoring of pressure and temperature provides early warnings of anomalies. Fluctuations in these parameters may signal equipment failure or hazardous overpressure conditions. AEP integrates advanced monitoring systems that deliver real-time data and alerts.
Safety Valve Maintenance
Pressure relief devices are vital for avoiding overpressure incidents. Regular calibration and testing are crucial for these mechanisms to operate effectively. AEP’s maintenance schedules include strict testing of all safety valves to ensure reliable performance.
Corrosion Management
Corrosion remains one of the primary threats to pressure vessel safety. AEP uses protective coatings, corrosion-resistant materials, and cathodic protection to mitigate this risk, extending the vessel’s service life.
Investing in Expertise and Training
Even the most sophisticated technology is ineffective without skilled personnel. AEP invests heavily in training our technicians to remain up-to-date with PED standards and the latest maintenance technologies. This ensures that our team can address complex challenges efficiently, safeguarding both safety and compliance.
Conclusion
In the European industrial landscape, preventing pressure vessel failure is a commitment to safety, operational efficiency, and environmental responsibility. At Alien Engineered Products (AEP), our PED-compliant pressure vessel solutions offer unmatched reliability, tailored to meet the stringent demands of the European market. By investing in preventive maintenance and adhering to global and regional standards, companies can avert catastrophic failures and optimize productivity.
Ready to elevate your pressure vessel maintenance strategy? Contact AEP today to learn more about our PED-compliant solutions and how we can support your business in maintaining safety and efficiency.