5 Benefits of Choosing Aluminum Welding for Industrial Applications
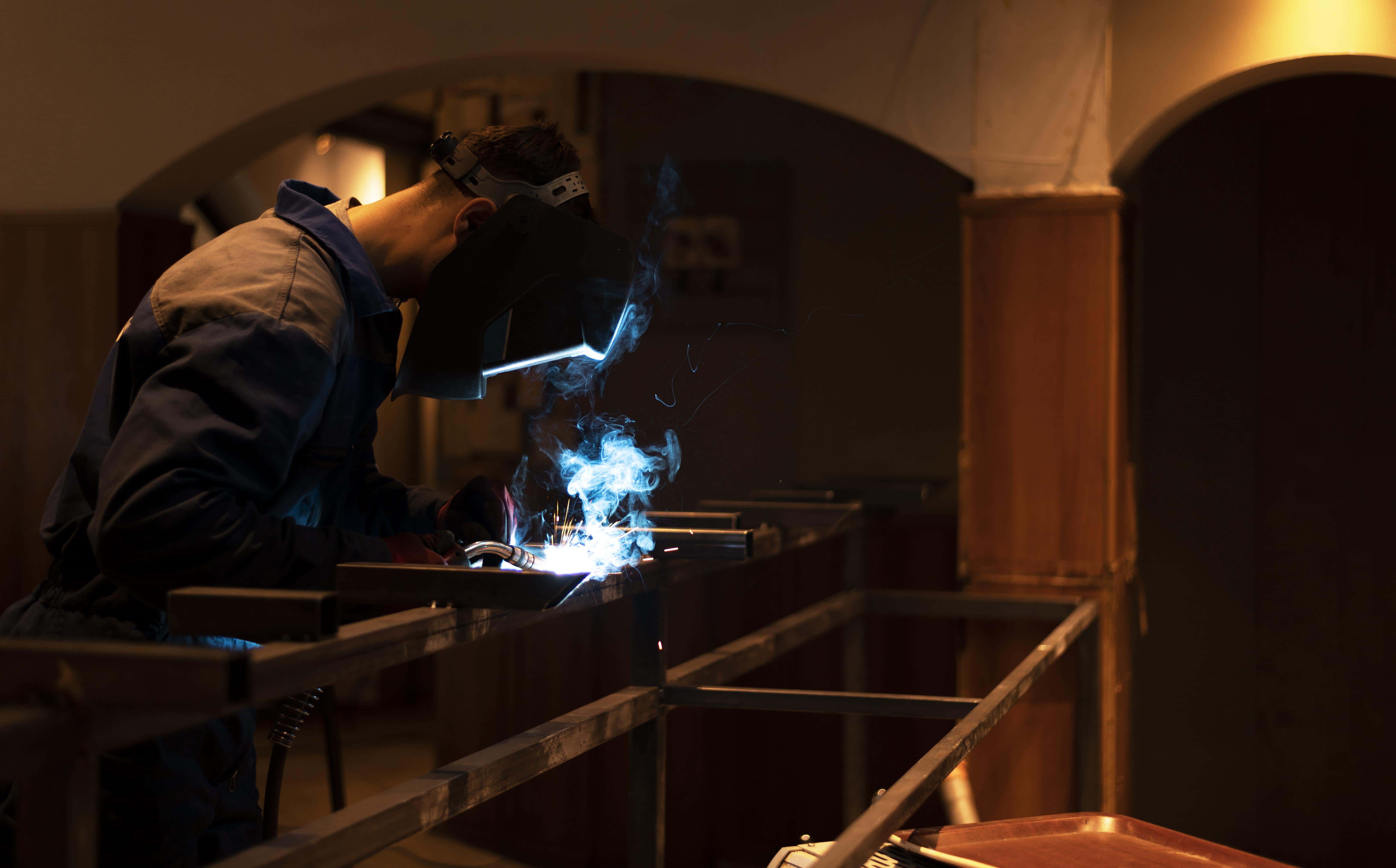

5 Benefits of Choosing Aluminum Welding for Industrial Applications
1. Lightweight Strength with Certified Durability
The exceptional lightweight-to-strength ratio of aluminum is one of its primary advantages, making it indispensable in industries like aerospace, automotive, and construction.
- Enhanced Structural Integrity
Welded aluminum components, when manufactured to ASME or PED standards, ensure high structural integrity even in demanding environments. Compliance guarantees that the welding process meets stringent material strength and load-bearing requirements. - Fuel Efficiency in Transportation
ASME- and PED-compliant aluminum welding is extensively used in transport industries across Europe and Australia to reduce weight without compromising safety. Lighter vehicles and equipment result in improved fuel efficiency and lower carbon emissions, aligning with regional environmental goals.
2. Superior Corrosion Resistance Backed by Standards
Aluminum naturally resists rust and corrosion, and when the welding process complies with ASME Section IX or PED specifications, this durability is further ensured.
- Durability in Harsh Environments
Industries in coastal areas or marine environments benefit greatly from aluminum's corrosion resistance. ASME- and PED-certified aluminum welds provide long-lasting protection against saltwater and chemical exposure, ideal for marine vessels, offshore rigs, and industrial tanks. - Cost-Effective Maintenance
Using aluminum welding that complies with PED and ASME ensures reduced maintenance costs by adhering to specific guidelines for material performance in corrosive settings. This is particularly valuable in Europe’s maritime hubs and Australia’s coastal industries.
3. High Thermal and Electrical Conductivity with Certified Precision
Aluminum's thermal and electrical conductivity makes it a preferred material for energy and electrical applications, particularly in projects requiring compliance with ASME and PED standards.
- Optimized Energy Solutions
ASME-compliant aluminum welding is frequently used in renewable energy systems like solar panels and wind turbines, ensuring efficient heat transfer. PED certification guarantees these systems meet Europe's strict energy performance requirements. - Safe Electrical Applications
For industries requiring electrical components, PED-certified aluminum welds ensure consistent performance and safety in applications like power transmission lines, control panels, and industrial machinery.
4. Sustainability and Environmental Compliance
Sustainability is a key driver in Europe and Australia, where regulations like the European Green Deal demand greener manufacturing practices. ASME and PED compliance further enhances aluminum’s eco-friendly appeal.
- Recyclable and Energy-Efficient
Aluminum is 100% recyclable, and PED-compliant welding processes ensure minimal environmental impact during fabrication. This helps industries meet sustainability goals and reduce their carbon footprint. - Compliance with Global Standards
Using ASME- and PED-certified aluminum ensures adherence to international environmental standards, facilitating smoother market entry across Europe and Australia.
5. Versatility and Adaptability with Certified Techniques
Aluminum welding’s versatility allows it to meet the needs of a wide range of industries, and certification by ASME and PED ensures that these solutions are safe, efficient, and reliable.
- Custom Solutions for Diverse Industries
ASME Section IX and PED regulations enable precise customization for industries like aerospace, automotive, construction, and energy. For example, PED-compliant aluminum welds are critical for pressure vessels used in European manufacturing. - Advanced Welding Methods
Techniques such as TIG (Tungsten Inert Gas) and MIG (Metal Inert Gas) welding are commonly employed for aluminum. When executed under ASME or PED standards, these methods provide optimal strength, accuracy, and quality assurance.
Why ASME and PED Compliance is Crucial
For industrial applications, compliance with ASME and PED standards is non-negotiable. Here’s why:
- Global Recognition
ASME standards are recognized worldwide, ensuring products meet the highest quality and safety benchmarks. PED certification is mandatory for pressure equipment sold in the European Union. - Enhanced Safety
ASME- and PED-compliant aluminum welding reduces the risk of failures, ensuring long-term reliability and performance. - Market Access
Compliance with these standards simplifies market entry and regulatory approvals in Europe and Australia, especially for industries involved in pressure vessel manufacturing, transportation, and energy.
Challenges in Aluminum Welding and How Standards Help
Although aluminum welding has challenges, such as its sensitivity to heat and the need for oxide layer removal, ASME and PED compliance ensure these are managed effectively:
- Heat Sensitivity: ASME-certified processes include precise thermal controls to prevent warping.
- Oxidation Issues: PED guidelines mandate pre-weld cleaning techniques to ensure strong bonds.
- Equipment Costs: Investments in certified welding equipment are offset by the long-term benefits of compliance and reduced failure risks.
Conclusion
Certified Aluminum Welding is the Future
Aluminum welding, when performed under ASME and PED standards, delivers unparalleled benefits in industrial applications. From corrosion resistance and sustainability to high conductivity and versatility, certified aluminum welding ensures superior performance and regulatory compliance.
By choosing ASME- and PED-compliant aluminum welding, industries can guarantee quality, enhance safety, and meet environmental and market requirements in Europe and Australia. Whether you are in aerospace, energy, or manufacturing, certified aluminum welding is the solution for your next project.
At Alien Engineered Products (AEP), we specialize in ASME- and PED-compliant aluminum welding for a variety of industrial applications. Contact us today to discuss how we can meet your project’s needs with our welding solutions.